Auto Mode Shift Point Table
This is not available if Auto Shift Option is set to Auto Disabled.
This is a special table which behaves differently to normal tables and uses special values in the left axis of the table.
The left axis of the table is locked to Auto Shift Point Axis, and the values are special values to indicate gear shifts. The values are simply like writing from_gear → to_gear. e.g. an up-shift from 1st to 2nd uses the special value 1 -> 2. A down-shift from 4th to 3rd uses the special value 4 -> 3. An auto-shift will only occur if it is listed in the left axis. e.g. if you want to allow auto shifting up to 3rd, but not to 4th, you might list 1 -> 2 and 2 -> 3 for up-shifts and 2 -> 1 and 3 -> 2 for down-shifts. A paddle shift request from the drive can still cause a shift into 4th.
How it Works
When driving around with Auto Shift enabled and the Gear Selector in a position which allows auto-shifts, this table is checked twice. Once to see if an up-shift should occur, and again to see if a down-shift should occur.
The up-shift check is done by checking to see if the up-shift is listed in the left axis of the table. If so, then the table value gets calculated for that up-shift. If the Main Shift Point Variable value is greater than the value in the table, an up-shift is requested.
The down-shift check is similar. If the down-shift is listed in the left axis of the table, the table gets calculated for that down-shift. If the Main Shift Point Variable value is less than the value in the table, a down-shift is requested.
e.g. if you're in 2nd gear, the table is checked to see if 2 -> 3 is in the left axis. If so, the table gets calculated for the value 2 -> 3 (e.g. 50 km/h). If the Main Shift Point Variable value (e.g. 55 km/h) is greater than this, an up-shift will be requested.
It will also check for 2 -> 1 in the left axis. If so, the table gets calculate for the value 2 -> 1. If the Main Shift Point Variable value is less than this, a down-shift will be requested.
Note that you don't need to list every possible combinations of gear shifts, only the single gear shifts. e.g. a typical 4 speed transmission will have 1 -> 2, 2 -> 3, 3 -> 4, 4 -> 3, 3 -> 2 and 2 -> 1. You don't need to include 1 -> 3, 1 -> 4, 2 -> 4, 4 -> 2, 4 -> 1, 3 -> 1. If you tick the Allow Gear Skip option, the ECU will automatically determine whether to shift multiple gears at a time by looking at multiple positions in the table. e.g. it might shift from 2nd to 4th if both the 2 -> 3 shift and 3 -> 4 shift points have been met. e.g. vehicle speed is 100km/h, 2→3 shift point is 40 km/h and 3→4 shift point is 70 km/h for the current load. The ECU will shift from 2 -> 4 if Allow Gear Skip is ticked.
When Engine RPM is the Shift Point Variable, you should ensure that the engine RPM drop from an up-shift won't cause a down-shift straight away when reaching the new gear. e.g. if 1st→2nd shift happens at 5000 rpm, and the difference in gear ratios brings the engine RPM down to 4000 rpm once in 2nd gear, the 2nd→1st shift point should be below this. Otherwise the Transmission Control function may continually keep trying to shift up and down between 1st and 2nd gears. This can be calculated by simply knowing the two gear ratios and the RPM you up-shift at. e.g. 5000 rpm * 1.63 / 3.06 = 2663 rpm after the shift. The down-shift point in the new gear must be less than this, otherwise a down-shift will be requested as soon as the up-shift is complete.
When Driven Wheel Speed, Driveshaft Speed or Driveshaft RPM is used as the Shift Point Variable, just ensure that the down-shift points are below the opposite up-shift points. e.g. if 1st→2nd shift happens at 50 km/h, the 2→1st shift must be less than 50 km/h. Otherwise the ECU will continually shift between 1st and 2nd gears.
Calculating Engine RPM Shift Points
Obviously, you could use trial and error and/or data-logs, but here's how to calculate it.
Full load up shift points for most spark ignition engines are simply the maximum possible engine RPM, as that's where they make most power. So you set the full load up-shift point just below the Main RPM Limit.
Partial load up shift points are more of an art-form which will require trial and error while driving the vehicle. Ensure that the engine RPM after a shift will be sufficient, by calculating what it will be. rpm_after = shift_point * current_ratio / target_ratio. e.g. 5000rpm * 1.63 / 3.06 = 2663rpm.
To calculate down-shift RPM points, choose the RPM you want to end up at when in the new gear. Call this target_rpm. Remember that there's not much point down-shifting if you end up very close to the up shift point, because when you get on the throttle again, some time will have to be wasted shifting up a gear. You're better off being at an imperfect gear ratio and saving the time of a gear shift.
Look up the gear ratios for your transmission. current_ratio is the gear ratio of the current gear. target_ratio is the gear ratio of the gear to down-shift to.
shift_rpm = target_rpm * current_ratio / target_ratio .
e.g. GM 4L60 down-shifting from 4th to 3rd with a target_rpm of 5000rpm. (4th gear has ratio 0.7 : 1 and 3rd gear has ratio 1.0 : 1 )
shift_rpm = 5000 * 0.7 / 1.0 = 3500.
Example Auto Mode Shift Point Table - Engine RPM for Racing
This is for a transmission with ratios of 3.06, 1.63, 1.0, 0.7. Main RPM Limit of 10,000 rpm, so up-shift point conservatively set to 9,500 rpm. Down-shift target RPM chosen to be 8,000 rpm.
This example is a racing application which isn't using load as an axis, just for simplicity. But all that needs to be done to convert this to a street application is to enable the top axis, put these values in the full load sites, and fill the rest of the table with lower values which should be tuned experimentally.
Calculating Vehicle Speed Shift Points
Obviously, you could use trial and error and/or data-logs, but here's how to calculate it. Note that these calculations assume no torque converter slip. If you're using a torque converter, either factor in the slip ratio, or configure your shift points experimentally.
For optimal gear shifts, you want to get the most power out of your engine. For petrol engines, this typically means shifting at the highest practical RPM.
Assuming you have calibrated the Vehicle Speed Sensors and the Gear Ratios (remember that you'll need the Torque Converter locked to do this, see Dyno Mode for details), this can be calculated very simply.
shift_speed = shift_rpm / 1000 * gear_ratio_setting_for_gear.
Example Auto Mode Shift Point Table - Driven Wheel Speed for Racing
I'll use the same example values as above with an imaginary final drive and tyre size to give settings of 9.8, 18.4, 30, 42.9. Up shift at 9,900 rpm and down-shift target rpm 8,000rpm.
Note that I'm assuming a locked torque converter in these calculations. If the torque converter is slipping, then the up-shifts will need to happen at lower vehicle speed to account for the torque converter slip.
up_shift_speed_1_2 = 9,900 rpm / 1000 * 9.8 = 97.0 km/h. Note that this uses the current gear's ratio, as you want to prevent over-rev.
down_shift_speed_2_1 = 8,000 rpm / 1000 * 9.8 = 78.4 km/h. Note that you use the target gear's ratio, as you're aiming to reach the target rpm in that gear.
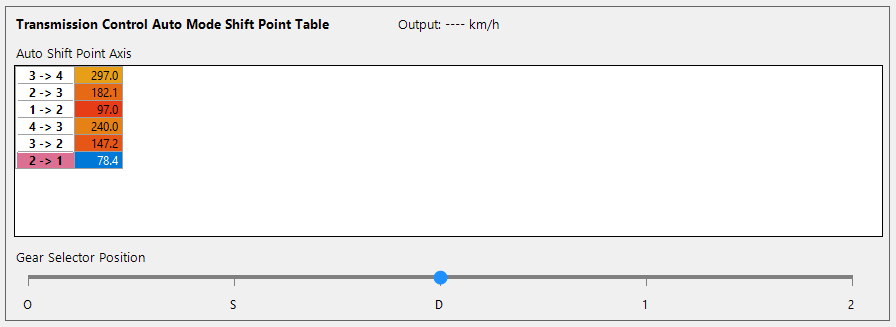