The MAP Prediction / Fuel Film Model allows the ECU to calculate the dynamic fuel delivery requirements of your engine during transient events such as rapid throttle movements and quick changes in load. This is actually two functions rolled into one due to their close relationship to one another. It is to be used as an alternative to the classic Transient Throttle function. When tuned properly the throttle response should be crisp, and the engine should react to changes in load without hesitation under all operating conditions.
At a very basic level, the functions work as such:
MAP Prediction: Uses a 3D lookup table to check the MAP value when the throttle movement is in a non-steady state. The ratio of the Measured MAP and Predicted MAP is controlled by the 'Transient TPS Scaling' setting. For example, if the throttle is rapidly snapped open, the ECU will derive the MAP value from the 'Predicted MAP' table while the rate of TPS movement is high (TPS Derivative), rather than from the actual MAP sensor itself (due to delays in this signal).
Fuel Film Model: Constantly models the film of fuel that exists between the fuel injectors and the intake valves. Based on the 'Film Pooling Percentage' and the 'Film Evaporation Time Constant' table values, the ECU will add or remove from this fuel film based on the engines changing fuel requirement. For example, if the calculated fuel requirement of the engine rapidly increases due to the throttle opening quickly, the ECU will add additional fuel to the fuel film to ensure there is adequate fuel for the increased load. The reverse of this is also true, where the ECU will remove fuel from the film when load is decreasing on the engine.
How it works
Looking at the functions at a more advanced level, there are 3 reasons that ECUs need to handle transient throttle conditions in a special way.
Reason #1: MAP sensor delay
MAP sensors themselves are fast, but to be able to have a useful MAP sensor reading, a significant amount of filtering needs to be applied. The pressure in the intake varies throughout the engine cycle as each cylinder does its intake stroke, so the MAP sensor signal must be averaged over at least one cylinder period. The Nexus ECUs average the MAP signal over either 1 or 2 cylinder periods, depending on the "Averaging Window" setting under "Engine Synchronous" on the Sensors page in the tree.
When the driver snaps open the throttle at idle however, the outside air rushes into the plenum very quickly; if the pressure ratio is > 2:1 then the air will actually go sonic. The plenum will be filled with air for a long time before the MAP signal registers this.
The MAP prediction method to deal with this problem is to have a Predicted MAP table, which gives the ECU an estimate (prediction) of the MAP to be expected at each RPM / TPS combination operating point. Then when the ECU sees a rapid throttle movement (determined by the Transient TPS scaling table), it uses the higher value either of the MAP sensor or the predicted MAP table, for as long as the Predicted MAP time setting dictates. This allows the ECU to use a less accurate, but more timely estimate of the MAP for fueling and other calculations.
Long Term Predicted MAP Learning
The ECU has a setting for long term predicted MAP learning. This fills out the predicted MAP table as the engine is operated, saving time for the tuner. It uses the fact that at any given RPM and TPS operating point, all the points at higher RPM and lower TPS will have a lower MAP value than the current operating point, and all the points with lower RPM and higher TPS will have a higher MAP value. The ECU samples the MAP when the ECU is not in MAP prediction, and "clips" the values in the table in these regions, either bumping the values up or bringing them down as required. The MAP value that's "learned" will be clipped at 101.3 kPaA, unless the aspiration method is selected as "supercharged" in "Engine Configuration".
Behavior in the event of MAP sensor failure
If the MAP sensor has a low level error, for example a DTC due to too high or too low voltage, or no I/O assigned to the MAP sensor, then the ECU will use the predicted MAP table to populate the MAP channel. This won't allow someone to drive a turbocharged car above atmospheric pressure, but it will allow gentle driving, and driving on NA or supercharged vehicles.
Reason #2: Fuel Pooling
On a port injected engine, not all the fuel delivered from the injector goes directly into the cylinder. Some percentage ends up on a film on the runner walls. This evaporates over time and gets sucked into the cylinder, so eventually all the fuel goes into the cylinder, but not all during the first inlet stroke. This means that in the steady state, the fuel calculations will be correct, but in transients, the ECU needs to account for the changes to the film volume. For example if the engine load increases suddenly, in the steady state the fuel film will be larger, so even more fuel must be injected to build up the pool. The two tables, pooling percentage and evaporation time, dictate the amount of correction that will be applied.
Reason #3: It's too late!
As mentioned in #1 above, on a throttle opening off idle, the air rushes into the plenum very quickly. This means that whichever cylinder (s) have their inlet valves open at the time will fill up with the new air amount as well. If the ECU is set up to do closed valve injection at idle, then the ECU has already delivered the correct quantity of fuel for the "old" manifold pressure. So any cylinders with open inlet valves at the time the throttle is opened will have a lean hiccup (there is always one on a 4 cylinder and two on an 8 cylinder).
The way around this that relies least on tuning time, gives a consistent result and is robust, is to instead perform open valve injection; ie retard the injection timing to 200-300° BTDC; instead of about 400°. One must be careful in optimising injection timing for transient response not to overfuel the engine - it is common for people to have too much enrichment as a band-aid to deal with a lean spike that happens due to incorrect injection timing, however it doesn't fix the actual problem. So start off with a small pooling amount and only increase it once the injection timing is optimised.
How to set up the MAP prediction based transient throttle
For this to work correctly, you need a functioning TPS (either cable or electronic) and MAP sensor (internal or external)
- Check that your TPS is operating correctly - ie, it moves smoothly through the range as the pedal is depressed, and doesn't jump around when the throttle is still
- In the Fuel Tuning menu, disable the Transient Throttle (Classic) function, and enable MAP prediction / fuel film.
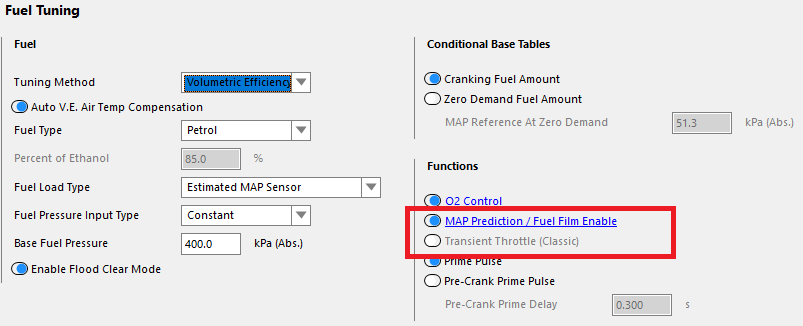
- Click the underlined name of the function to enter the menu.
- Start with the default values in the default map. If you want to restore the defaults for the predicted MAP section, select "Restore Defaults" from the File menu and select the MAP prediction / fuel film settings:
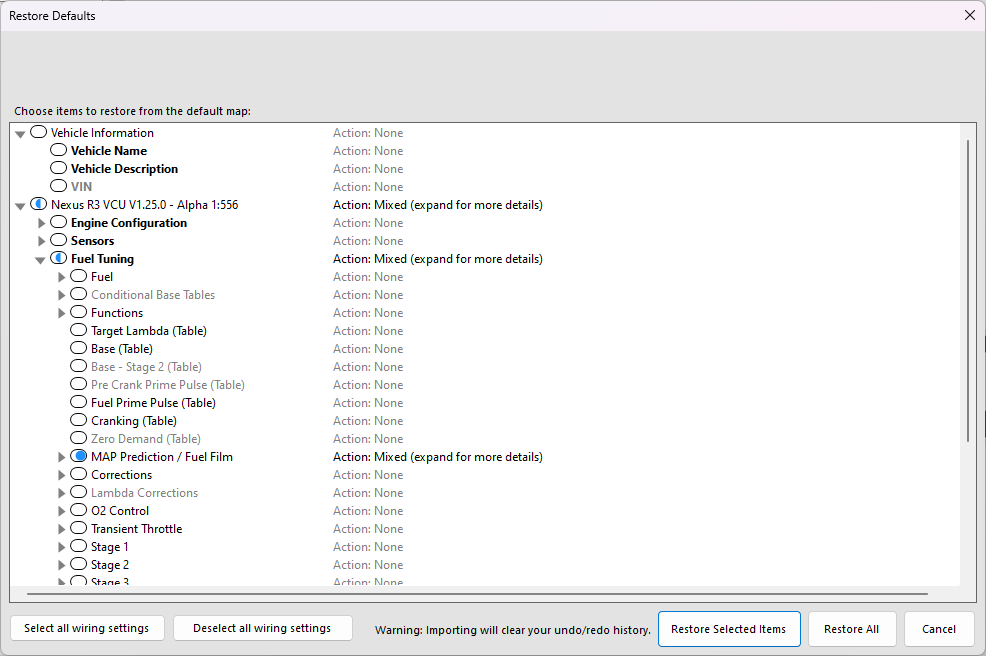
- Optimise the injection timing at idle for the best off-idle transient response. This is normally around 270 - 330 degrees BTDC - so in the open valve condition (for reasons explained above).
- With predicted MAP long term learning turned on, you should not need to touch the predicted MAP table. However after doing some driving (or visiting the cells through the normal tuning process) you should check the table to make sure it matches the MAP that the engine achieves in the RPM/TPS combinations.
- Once the predicted MAP table is learned, the two parameters that may need adjusting are the Film Pooling Percentage, and the Film Evaporation Time Constant. The pooling amount is the adjustment to change how much correction is required - in general use as low a value as you can get away with that "feels good". The evaporation time constant is the adjustment for how long the extra fuel is added in an enrichment situation.
Typical values to expect
Predicted MAP time: Usually around 200ms. If it's too short, then when you do a throttle stab, the predicted MAP period will be over before the real MAP sensor has caught up. This will require a longer time if the MAP hose is long or shared with other sensors or gauges (not recommended)
Film Pooling Percentage: As low as 5-10% for a well matched intake port and injector, on gasoline, when the engine is warm. Around 25-30% for an engine with sharp inlet turns and injectors not spraying into the chamber (eg side port rotary), or mismatched injector and head (eg using a single spray injector on a 2-inlet valve head - the fuel hits the divider). Around 50% or even a bit more when the engins is cold (less fuel evaporation).
Film Evaporation Time Constant: Typically 200ms when engine warm, as high as 400ms with a cold engine.
How to Tune based on symptoms
Predicted MAP state doesn't transition to "active" when you press the throttle, or press it gently
- Check that TPS is operating correctly
- Monitor the TPS-d (Throttle Position Derivative) channel
- Set the Transient TPS Scaling table to a value about 10 times the normal range that you see of the TPS-d channel with the throttle closed. Eg if it's normally in the range of ±10%/sec, set the sensitivity to 100%/sec
Predicted MAP state is triggering under constant throttle conditions
- Check that the TPS is operating correctly
- Increase the Transient TPS Scaling table
- Check that the predicted MAP table is filled out with the steady state MAP values
- Check that the fuel map is tuned to the correct values in the steady state
- Adjust injection timing - normally around 300° BTDC gives enough time for the injector to deliver a pulse at idle, but late enough that the ECU can respond to a rapid air change
Goes too rich on throttle transition, after throttle applied (50 - 150ms)
- Reduce the fuel pooling value in the map
Goes too lean on throttle transition
- Check that the predicted MAP table is filled out with the steady state MAP values
- Check that the fuel map is tuned to the correct values in the steady state
- Check that injection timing has already been optimised to give the best response
- Increase the fuel pooling value in the map
Behavior in the case of MAP sensor failure
- If the MAP sensor has a low level error, for example a DTC due to too high or too low voltage, or no I/O assigned to the MAP sensor, then the ECU will use the predicted MAP table to populate the MAP channel. This won't allow someone to drive a turbocharged car above atmospheric pressure, but it will allow gentle driving, and driving on NA or supercharged vehicles.
Effects on Closed Loop O2 Control
- Closed loop O2 control will be disabled while MAP prediction is active; the reason given will be "Transient throttle"
- Closed loop O2 control will be disabled during the MAP sensor failover to the predicted MAP; the reason given will be "MAP sensor failure"
Channel Reference
- Predicted MAP active: Whether the ECU is currently in MAP prediction or not. This is based on the TPS derivative compared to the TPS scaling. At this value, the ECU uses the full predicted MAP amount, and at lower throttle transient rates it is scaled down so that less "prediction" occurs. Below 25% of the value in the TPS Scaling table, no MAP prediction is triggered. In the event of MAP failover, the state will be given as "Used because of MAP sensor error"
- Unfiltered Manifold Pressure: The raw "live" value from the sensor - without any filtering
- Measured Manifold Pressure: The filtered value from the sensor, filtered between TDC events (either 1 or 2 cylinder periods)
- Manifold Pressure: This is the ECU's estimate of MAP, either from the measured manifold pressure or the predicted MAP table or a blend of the two
- Fuel - Film Model Correction: This is the percentage of fuel change based on the fuel film model. If the ECU is injecting an extra 10% of fuel than it would in the steady state to make up for the lack of fuel in the film, this channel will read 10%.