We all know that one keyboard warrior who brandishes their dyno sheet like a boy scout merit badge. But what does that big fancy number even mean in the real world? How does his/her car perform compared to others? And more importantly, does that three or four-digit number even matter?
So, let’s dive deeper into power curves and how their results can tell us a story about a particular engine or car’s habits. For a TL:DR version, check out Scott’s video linked above!
What is power?
To clear up some confusion, “power” and “work” are different terms. Power is the rate at which we perform work; Work is the action itself. Meaning, if we lift a 20-pound weight to a height of 10 feet in one second, we generated 200 foot-pounds per second of power.
Okay, but where does horsepower come from?
Well, James Watt (guy who helped design the steam engine) decided we need a common unit of measurement to determine power. Through testing, he established that a horse could lift 550 pounds at a rate of one foot per second. Thus, the term “Horsepower” was born.
That’s great! Now we have a unified standard for measuring power, but what if the work being performed is rotational (ie. Driven wheels, or spinning crankshaft)? We can calculate that by multiplying “torque” (rotational work) and speed (RPM), then dividing that value by 5252.
Wait, 5252?
Don’t worry, think of this as a constant figure used to convert units into something recognisable. Engine speed is measured as # of revolutions per minute (RPM), but Mr. Watt defined horsepower as 550 foot-pounds over one second. Add on the fact we are measuring speed and not distance, it becomes apparent that this conversion is needed. Here’s a quick breakdown:
We know 1 horsepower is equivalent to 550 foot-pounds per second. Our dyno measures power in torque and engine speed, but we need to convert these values to our foot-pounds per second unit.
One minute is equivalent to 60 seconds, that’s understood. But, how do we account for length without a measured distance? With a radian. Think of it as a ratio of the radius of a circle versus a set length of the circumference (outside edge). Since we are measuring one revolution, that arc is equal to its radius (the same as multiplying by 1).
Wait, what? Yeah, that radian is equivalent to multiplying by 1 and this applies to all circles (because by definition they’re 360 degrees). So let’s convert that RPM to RPS (seconds) by multiplying it with the circumference (which has a radius/length of 1). Then convert minutes to seconds by dividing by 60. Voila, we now have 0.10472 RPS.
Now we have the ability to convert that 550 foot-pounds per second into a common value. Divide our 550 by the 0.10472 RPS to get…. 5252.
How do we measure it?
If you’re reading this, then you’re most likely an automotive enthusiast. This means you have at least heard of a chassis dyno. But what are they and how do they convert screaming exhaust into a figure we can understand and tell our buddies about?
Dynamometers usually come in two flavours, the first and most simple are inertia dynos. These are essentially a very large, heavy steel drum that a vehicle is strapped too and calculate how fast you can accelerate that drum (quicker it is spun, the more horsepower you’ve made). They’re very useful for back-to-back power runs and for mechanical fuel tuning (carbureted engines).
The second and more useful type is known as a load-bearing (steady-state) dyno. They provide you with the ability to hold an engine at a steady RPM and measure the torque output in real-time. This gives tuners the opportunity to tune specific fuel cells for a more complete table.
For a more in-depth look at the various types including chassis, hub and engine dynos, be sure to check out Scott’s Dyno Tuning Basics video below:
Looking at our own Mainline steady-state, we see the rollers themselves. The larger rollers spin freely and just help keep the tyre in place during a run.
The smaller, knurled rollers (rough, machined surface for traction) are attached directly to a retarder shaft. This shaft is slowed (retarded) by an Eddy current brake, which is a large electromagnetic brake that is powered to generate drag/load on the shaft.
Do you see that blue bracket off of the eddy brake? That’s attached to the load cell, which calculates the amount of force that the roller is being subjected to.
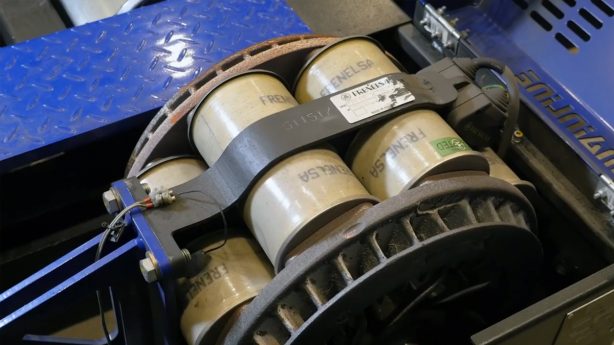
There are variables such as heat, momentum, and mechanical loss taken into account when the final numbers are being generated.
But in essence, with speed (RPM of the roller) and force (effort on the load cell) the computer can calculate the horsepower being generated against our chassis dyno.
What do we do with it?
Great, now we know what horsepower is and how it’s measured. But what are you supposed to take away from that fancy dyno sheet, what have you learned? Let’s have a look at a pull recorded on our dyno with a naturally aspirated four-cylinder engine.
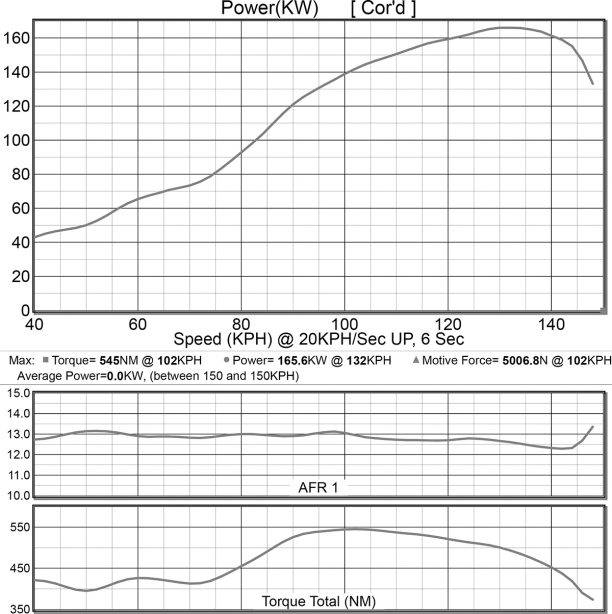
This pull was done from a speed of 40 KPH – 150 kph, with the dyno only allowing a 20 KPH increase every second (for a total of 6 seconds). Notice the traced line in the top graph, this represents the horsepower output over the run. We see a total peak output of 165KW (~221HP) which is a respectable number for a non-power adder four-banger.
But, what’s more important is the shape of the overall curve. Think of this powering a daily driver, we wouldn’t see a huge delay in performance, it would be pretty responsive when accelerating from a low speed (imagine merging onto an interstate). No matter where we are in the graph, you could expect this engine to produce at least 45-50KW (~65HP) at the wheels. Which in a small vehicle would be plenty of power to move out of its own way.
Okay, great, but what would happen if we threw some boost at it?
Let’s have a look at a turbo R32 GTR. This is a modified inline 6 with a larger than OE turbocharger. Using the same pull/load (20KPH/sec), we see a very different curve shape. While the peak power output is 520KW (~710HP), triple what our four-cylinder engine made, you can see that the majority of that power did not show itself until around 140KPH.
If this were a road-driven car, the smooth, yet lower power delivery of the four-cylinder would be much more enjoyable. But in a drag racing scenario, the sluggish inline-six would be an absolute riot at higher RPM/speed. This is why it’s important to choose an engine combination that suits your vehicle’s purpose.
Why is the “area under the curve” important?
Let’s look at the four-cylinder dyno graph again; we know that the line represents output over the entire run.
The area underneath that line is the total amount of effort (work) our engine produced. When we say we are looking to maximize the area under the curve, it means that we are looking to generate as much work/power throughout the entire rev-range. The larger the area under the curve, the more power we are making.
Why do we want it?
Okay, imagine we have a drag car with launch control, a modified differential and a racing-oriented transmission. This vehicle’s purpose is to generate maximum power to the track surface as fast as possible. Would it be worth the effort to generate large bottom end power, or could we focus on fine-tuning the engine to deliver horsepower at a specific higher-RPM band?
If we have the ability to utilise tools such as a 2-step and transbrake (both can be controlled with a Haltech ECU, by the way), then it’s possible to help isolate the engine’s power band. Think about the R32’s dyno sheet, that massive delay in power can be avoided/ignored with a few tricks. By keeping the engine in an area where it’s generating its highest Total Torque value, we know it will exert as much force as possible.
The Takeaway
Alright, what did we learn from all of this? That horsepower is a relative thing, and how fast your car is, depends on much more than just a dyno pull. Sure, there will always be keyword warriors who claim their big number as gospel. But looking at the overall shape of the curve gives a better understanding of where and how your engine will make power.