In Gear Base Duty
This sets the Base Duty Cycle of the Line Pressure when the Transmission Control function is holding the transmission in gear.
If using Open Loop control: this is the duty cycle used.
If using Closed Loop control: the PID control plus the result of this table is the duty cycle used.
Axes and Setup
Because most transmissions are built to be as fail-safe as practical, the line pressure actuation is typically done so that if there's an electrical failure, the car can still drive. As such, when 0 current flows through the line pressure control solenoid, full line pressure is achieved. The line pressure control solenoids are typically built in such a way that increasing current decreases line pressure.
If you are tuning in open loop mode, you will typically tune this table with one axis representing the amount of torque the engine is producing (e.g. Load - Normalised Air Mass Flow, Manifold Pressure, Engine Demand or Throttle Position), and the other axis will be Gear.
If you are tuning in either Open Loop w/ Target or Closed Loop mode, then the Duty Cycle table should have one axis set as Line Pressure Control Target Pressure, and the other axis should be Transmission Oil Temperature, since temperature significantly affects the resistance of the line pressure control solenoid. You could use Battery Voltage instead of Transmission Oil Temperature, but it is far less variable once the engine is running. You want to configure the Duty Cycle table before tuning.
Tuning Tips
If you are tuning a transmission which has a base map provided, then it is recommended to import the Line Pressure Control settings from that base map. Otherwise you'll have to fill out the table yourself. Below is an example of how to do it.
There are multiple ways to get this table set up, depending on what you have available.
Using Line Pressure Sensor
This is the simplest way and most accurate way to configure the duty cycle tables. It obviously requires a Line Pressure Sensor to be installed, enabled and calibrated. Simply change the duty cycle until the Line Pressure channel reads what you want it to read. Start from high target pressure, low duty cycle, and increase until you achieve your target.
Note that the engine must be running in order to cause the transmission fluid pump to turn and create pressure. Sometimes idling is sufficient, but you may need to hold the engine RPM constant at cruise RPM if idling cannot create sufficient pressure.
Using multi-meter measuring current
This is the next best method, but requires information about the line pressure control actuation, such as this table, which can sometimes be found in the workshop manual of the vehicle the transmission is from. This can be done with the engine off.
Typically you will set the table to have Line Pressure Control Target as one axis, with values from the Amperage to Line Pressure table. If a range is in the manual, use the average to get an approximation : (low value + high value) / 2. e.g. (1103kPa + 1241kPa) / 2 = 1172kPa.
Be aware that manufacturing tolerances mean this won't be exact, but these values should be good enough for you to tune with. If you want more precision, install a Line Pressure sensor and use the method above.
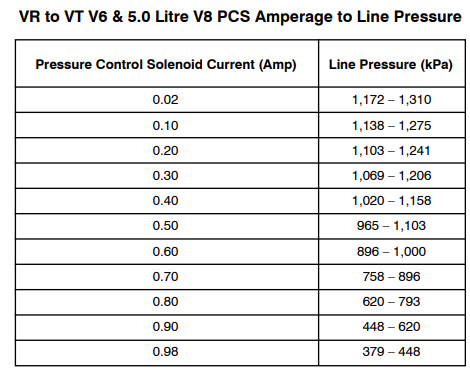
You will need to connect a multi-meter in series with the solenoid. The easiest way to do this is by pulling the ECU pin out and temporarily connecting it to the red probe, and putting a temporary wire with pin to the ECU connector. The temporary wire will need to be connected to the multi-meter black probe. See below for rough wiring guide. Start with low duty cycle in the site which will require lowest current (typically highest target pressure). Increase the duty cycle until the multi-meter measures the current in the table.
Calculating the theoretical duty cycle
This is the least accurate method, but this isn't critical, as you'll tune around it anyway.
Measure the resistance of the solenoid when the transmission fluid temperature is at the site(s) you wish to tune for. If you only tune for one temperature, this should be the typical operating temperature, which will be around 100°C / 212°F. Only tuning for when hot will result in non-ideal behaviour when cold.
If you can't measure the resistance, you can use average values from the workshop manual as a very approximate value. e.g. this solenoid has 4 to 7 ohms resistance at operating temperature. Average is 5.5.
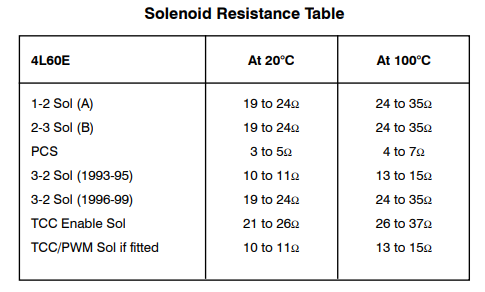
For each site in your table, calculate the duty cycle as follows:
Use V = IR to calculate the effective voltage needed to get that current. The current is from the Amperage to Line Pressure table from the workshop manual. e.g. V = 0.98A * 5.5 Ω = 5.39V.
Calculate the required duty cycle. Duty Cycle = 100% * effective voltage / supply voltage. For supply voltage, look at the Battery Voltage channel while the engine is running. Ideally at cruising conditions. e.g. Duty Cycle = 100% * 5.39V / 13.8V = 39%.