The LS2 engine will be referenced throughout this guide unless a specific LS3 difference is noted.
Holden Commodore VE LS2 L98 engine
The LS2 family are a V8 with an alloy block
Number of Cylinders
| 8
|
Capacity
| LS2 5967cc (364ci)
LS3 6162cc (376ci) |
Firing Order
| 1,8,7,2,6,5,4,3 |
Cylinder Orientation | (1357 RHS) |
Model Variants
LS2
6.0L, 10.9:1 comp, cathedral port heads
LS3
6.2L, 10.7:1 comp, rectangular port heads (higher flow than cathedral)
L76
6.0L, Aussie version LS2, DOD Cylinder Shutdown, rectangular ports
L98
6.0L, rectangular ports, very mild cam
LS7
7.0L, steel crank, Ti rods, dry sump
LSA
6.2L Supercharged, 9.0:1 comp
LS9
6.2L Supercharged, 9.1:1 comp, larger supercharger
LQ9
6.0L 10.0:1 comp, Cast Iron block
LSX
6.0L, cast iron block with thicker walls, extra head stud per cylinder, improved main bearing oil supply, doweled 6-bolt mains
Trigger System
The LS2 engine has a trigger system mounted on the crankshaft that has a 60-2 tooth pattern. This refers to there being 60 total teeth with 2 that are missing with the missing gap used as a sync point for the ECU. It is not the gap itself that is the trigger point, the ECU uses the first tooth after the missing tooth gap to time the engine. Some in the industry refer to this pattern as a 58x. It is an improved design over the Gen3 24x pattern as it removes issues related to "edge swapping" when large camshafts are fitted. The engine can also half-sync and run from the crank sensor alone also aiding with redundancy.
The camshaft has a 4x tooth pattern with 2x small and 2x big teeth.
LS2 Crankshaft showing crank trigger system
LS2 camshaft sprocket showing 4x trigger system
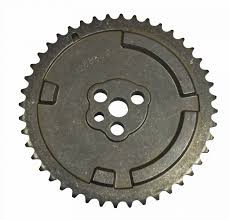
Crank Sensor
The Gen 4 engine uses a normal Hall Effect Sensor even though many in the industry refer to it as a Reluctor sensor. It is located above the starter motor towards the rear of the engine block. Gen 4 sensors are grey, Gen 3 sensors are black and of a Reluctor type (with internal signal conversion to output as a Hall) and cannot be used with a Gen 4 crankshaft trigger pattern.
Crank Sensor Pin
| Haltech Connection
|
A
| Trigger + (Yellow) |
B
| Signal Ground (Blue)
|
C
| 12V+ (Red) |
Cam Sensor
The LS2 Cam Sensor is of a normal Hall Effect type. For Gen 4 engines it is located at the front of the engine in the timing cover.
Some have an extension cable.
From the Haltech Terminated Harness Quick Start Guide

Wiring Info for VE Commodore L98 6.0L from the OEM workshop manual
Trigger Configuration
Injection System
All LS2 engines operate under sequential injection with an injector located in the inlet manifold spraying directly onto the intake valve. Injectors are High Impedance. The fuel system is of a non-returning type run at a fixed fuel pressure. Injectors flow around 350cc/min
LS3 ~ 420cc/min
Ignition System
LS2 engines operate as Direct Fire with a coil per spark plug mounted on the rocker covers of the engine. These coils have internal igniters and can be wired directly to the Haltech ECU. There are two common types of coils, the normal LS2 and the LS2 Truck coil.
LS2 Coil
Pin Letters are on the Connector Shell
Pin | Connection |
A | Ground (Cylinder Head) |
B | Ground (ECU Signal Ground) |
C | Ignition Output |
D | 12V+ |
It is advised to Ground both pins A and B to the Cylinder Head to avoid grounding issues causing damage to the coils.
Set to Constant Charge with Falling edge. Using Rising edge will damage the coils.
There are no timing marks on LS engines. To verify ignition timing new marks need to be added for TDC. To do this a piston stop tool is required.
LS2 Truck Coil
These are identified by a large heat sink. Wiring is the same as for normal LS2 coils.
Dwell Time
Charging LS2 coils at over ~5ms can lead to them auto-discharging which results in random ignition timing. It appears to be an issue with "break" time, the time between firing events. With high dwell time they will run fine at low rpm, but as rpm is increased issues can be seen. Care should be taken to not overcharge these coils especially at higher RPM.
Suggested Dwell Time for LS2 Coils
Drive By Wire (DBW) Throttle System
The LS2 uses a single Drive By Wire throttle body. This can only be controlled by an Elite 2500 or 1500 model ECU.
DBW Accelerator Pedal Position Connection
Pin
| Description
| Haltech Connection
|
1
| 5V+ | 5V+ |
2
| 5V+ | 5V+
|
3
| Signal 1 | AVI4
|
4
| Ground | Signal Ground
|
5
| Ground | Signal Ground
|
6
| Signal 2 | AVI5 |
Throttle Position Sensor
A cable throttle can be used with an LS2.
Pin
| Description
|
A
| 5V+
|
B
| Signal Ground
|
C
| Signal
|
MAP Sensor
The LS2 engine comes with a MAP sensor located on the inlet manifold.
Pin
| Connection
|
1 | 5V+ |
2 | Signal Ground
|
3 | Signal (AVI)
|
A number of different MAP sensors have been used on LS2 engines. Some are 1.0-Bar, 1.3-Bar, and 2.0-Bar depending on the model.
Calibration files for most are included in the ESP software
LS3 MAP Sensor
Part # 0 261 230 282
1.3 Bar
Idle Control
Idle control is handled by the DBW Throttle System for those engines so equipped.
If a cable throttle is used these will have a stepper motor idle valve. This is only supported on the Elite 1000 and higher ECU models.
It is not supported on Elite 550, 750, or 950 ECU models.
Pin
| Haltech Connection
|
A
| Stepper 4
|
B
| Stepper 3
|
C
| Stepper 2
|
D
| Stepper 1
|
Drive Type: Both
Steps:240
Speed:75
Coolant Temperature
Located on the LHS cylinder head near cylinder 2 exhaust pipe.
Uses Delphi connector that requires the wire to be fed through the connector first, the pin crimped, and then pull back to lock the pin in place.
Wiring is not polarity sensitive
Calibration: Use "Temperature - Holden VP V8 Coolant Sensor.cal"
Created for Haltech ECUs using a 1k pullup to 5V
Air Temperature
Located as part of the MAF. See MAF section for Wiring Information.
Calibration: Use "Temperature - Holden VP V8 Air Sensor.cal"
Created for Haltech ECUs using a 1k pullup to 5V
O2 Sensor
The LS2 comes with 4x 4-wire narrowband O2 sensors. It is strongly recommended to replace the front O2 sensors with a wideband O2 kit such as the Haltech WB2.
O2 Sensor Wire Colours
| Haltech Connection
|
Black (Signal)
| AVI 1 or AVI 6
|
Grey | Signal Ground (Black/White) |
White | 12V+ Switched |
White | Chassis Ground (not Signal Ground) |
Most narrow band O2 sensors use a black wire for signal. This is often mistaken as the ground wire.
The heater wires are not polarity dependent. The heater ground can be pulsed with an ECU output. Use an Injector, Stepper, or DPO for this. DO NOT USE an Ignition output.
Knock Sensor
The LS2 has 2x non-resonant style knock sensors located on the outside of the block on each bank. These can be used with the Haltech ECU.
Oil Pressure Sensor
The LS2 engine incorporates an Oil Pressure Sensor located on the oil filter housing.
Wire colours may vary with region or vehicle
Pin
| Connection
|
A | Signal Ground (Green) |
B | 5V+ (Blue/Yellow) |
C | AVI Signal (Blue/White) |
Calibration: Use "Oil Pressure - GM LS1 Stock Sensor.cal"
0.5V = 0psi 4.5V=130psi
MAF Sensor
Commonly deleted when a Haltech ECU is installed, however it can be used if preferred.
The MAF also incorporates an Air Temperature Sensor
MAF Connection
| Haltech Connection
|
A - MAF Signal
| Any Spare AVI |
B - 12V+
| 12V+ |
C - MAF Ground | Signal Ground (Black/White) |
D - Air Temperature Signal | Any Spare AVI (AVI7 typical) |
E - Ground | Signal Ground (Black/White) |
Automatic Transmission
6L80E
The 6L80E 6-speed transmission requires ECU control over CAN. It is built by GM and is listed to be a ZF 6HP with a different gear set.
Common Issues
Trigger Errors
With a cam swap it is common to have issues with the cam sensor signal occurring too close to a crank sensor edge. If the cam sensor edge swaps from before to after the crank sensor edge, or vice versa, an engine position error will occur. Monitoring the Home Percentage of Valid Travel channel shows how close the edges are to each other. If it is too close to either 0 or 100% then this can occur with a running engine.
Possible solutions are:
1. Try a different cam edge. This requires a TDC Offset change of 360, so either adding or subtracting this amount while keeping the value between 0 to 720.
2. Try adding filtering to the Home. Increasing to 2 or 3 can delay the Falling edge enough to keep it away from the crank sensor edge. The higher the rpm, the high the Home % channel will report.
Incorrect Trigger Pattern
Mixing of Gen 3 and 4 parts can be common when a custom engine is assembled. Most combinations will work however there is one combination that cannot work.
Crank Trigger Pattern | Cam Trigger Pattern | Will it Work | Configuration Trigger Type |
24x Gen 3 | 1x Gen 3 | Yes | General Motors - LSx Gen III (24x + 1x) |
24x Gen 3 | 4x Gen 4 | No | --- |
60-2 (58x) Gen 4 | 1x Gen 3 | Yes | Generic Missing Tooth Single Tooth Home
Trigger Signal Location = On Crank Number of Teeth = 60
Number of Missing Teeth = 2 |
60-2 (58x) Gen 4 | 4x Gen 4 | Yes | General Motors - LSx Gen IV (58x + 4x) |
If the engine is yet to be built and a decision is to be made as to which trigger system is best, the Gen 4 trigger is a better option that allows a wider range of cam position movement before trigger errors are an issue. The missing tooth crank trigger also provides a higher level of redundancy as well as faster sync and engine startup.
It is possible to have an incorrect crank position sensor installed. The black sensor from the Gen 3 motor cannot be used with a Gen 4 crank trigger wheel. The trigger pattern and sensor type must both match.